Welding is a critical process in many industries, from automotive repair to construction. The right welding machine can make all the difference in the quality and efficiency of your projects. With over fifty years of expertise, Car-O-Liner is a leader in welding technology, providing advanced and reliable equipment to meet diverse welding needs.
In this guide, you’ll learn about the various types of welding machines, their unique features, advantages, and ideal applications. Whether you’re a hobbyist or a professional, understanding these machines will help you choose the best one for your projects, ensuring high-quality welds and successful outcomes.
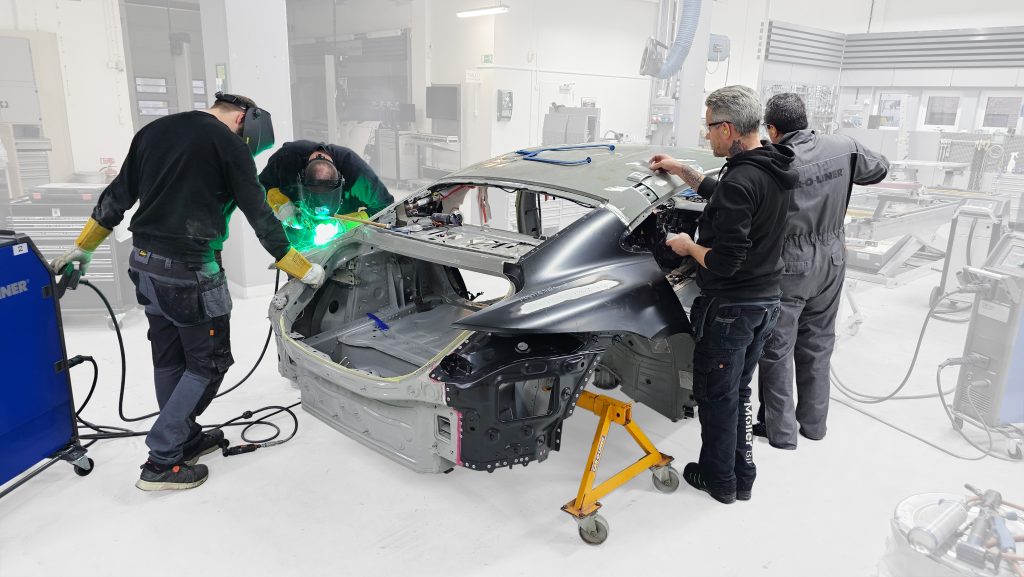
What is Welding?
Welding is a transformative process that creates permanent bonds between materials, most commonly metals and thermoplastics. It achieves this by applying intense heat to the materials, causing them to melt and intermix, forming a powerful connection. This molten pool often incorporates a separate filler material, which melts alongside the base metals, further strengthening the joint as it cools and solidifies. The resulting weld is frequently stronger than the original material itself.
Welding is used extensively across various industries because it creates durable and long-lasting connections. In automotive repair, welding plays a critical role in restoring the structural integrity of vehicles after a collision. By rejoining fractured frames and body panels, welders ensure the safe repair of the car and its return to the road.
Similarly, the construction industry relies heavily on welding to construct strong frameworks for buildings, bridges, and other structures. Welded joints provide the necessary strength to withstand significant loads and stresses, ensuring the safety and stability of these structures.
The aerospace industry takes welding to another level, as it’s crucial for building airplanes, spacecraft, and other vehicles designed for flight. In this demanding environment, welds need to be incredibly strong and lightweight to guarantee the safety and performance of the aircraft.
Types of Welding Machines
Now that we’ve explored the fundamentals of welding and its role in vehicle repair and other industries, let’s delve into the exciting world of welding machines! Each machine offers unique capabilities and caters to specific applications. Understanding these distinctions will empower you to choose the right tool for your welding needs.
Here’s a breakdown of some of the most common types of welding machines:
MIG Welding Machines
MIG (Metal Inert Gas) welding is a popular choice for both beginners and experienced welders due to its user-friendly nature. It’s a type of arc welding machine that works by continuously feeding a consumable wire electrode that acts as both the electrode and filler material.
An inert gas, typically argon or a mixture of argon and carbon dioxide, surrounds the weld zone. This gas acts as a shield, protecting the molten metal from air contamination and ensuring strong, reliable welds on a wide range of metals, including steel, stainless steel, aluminum, and even thin sheet metal. MIG welding also offers a variation called pulse welding. This provides improved control and reduced spatter, making it ideal for working with thin materials.
MIG welding equipment shines in terms of ease of use. The continuous wire feed simplifies the process, reducing the learning curve for beginners. Additionally, a MIG welding machine’s versatility allows it to tackle a wide range of projects and metals. It excels at producing fast welds, making it a valuable tool for applications where efficiency is crucial.
However, MIG welders do come with some limitations. The initial investment can be higher compared to other options. Their portability is restricted by the need for a gas canister, making them less suitable for situations requiring frequent movement between work sites. Regular maintenance is also necessary for optimal performance, which includes cleaning the torch and replacing the liner to ensure smooth wire feed and consistent gas flow.
Despite these drawbacks, MIG welders remain popular due to their ease of use, ability to handle diverse materials, and impressive welding speeds. They are a valuable tool for both beginners and experienced welders in various applications, such as auto body repair, home renovations, and hobbyist projects.
View our line of MIG Welding Machines
MAG Welding Machines
Like MIG welding, MAG (Metal Active Gas) welders utilize a continuously fed wire electrode. However, they differ in the shielding gas used. MAG welders employ a more reactive gas mixture, enabling them to handle a wider range of metals compared to MIG welders. This makes them particularly useful for working with galvanized steel and other metals that can be challenging with traditional MIG welding due to oxide formation on the surface.
In addition to versatility, MAG welding offers advantages like speed, quality, and cost-effectiveness for applications like auto body work and hobbyist projects. However, there’s a trade-off for this versatility. MAG welding requires a higher level of skill compared to MIG welding due to the reactive nature of the gas.
The reactive gas is more sensitive to air contaminants, so maintaining a clean work environment is crucial for achieving optimal weld quality. Additionally, MAG welding is not ideal for outdoor use because wind can affect the shielding gas, potentially compromising the weld.
View our MAG Welding Machine
TIG Welding Machines
TIG welding (Tungsten Inert Gas) is renowned for its precision and control, making it a preferred choice for intricate and high-quality welds. This method employs a non-consumable tungsten electrode to create the weld, while an inert gas, typically argon or helium, shields the weld area from atmospheric contamination.
The standout feature of TIG welding is the exceptional quality of its welds. This technique allows for meticulous control over the welding process, making it ideal for projects that demand fine detail and precision. The resulting welds are not only clean and strong but also visually appealing. This makes TIG welding especially suitable for working with thin materials, where precision is crucial to avoid burning through the material.
On the downside, using a TIG welding machine requires a high level of skill and experience, which can be a barrier for beginners. The process is also slower than other welding methods, which can be a disadvantage for larger projects. Additionally, TIG welding equipment tends to be more costly, which might be a consideration for those on a tight budget.
Nevertheless, TIG welding remains indispensable for applications that require superior precision and quality. It is frequently used in automotive repairs, intricate metalwork, and projects involving thin materials where control and detail are paramount.
Resistance Spot Welding
Resistance Spot Welding (RSW) is an efficient and robust welding method widely used in industrial settings. It operates by passing a high electric current through metal sheets, creating resistance and generating heat, which melts the metal and forms a weld. This technique is particularly effective for joining thin metal sheets.
One of the primary benefits of a spot welder is its speed and efficiency, making it ideal for high-volume production environments. The welds produced are strong, ensuring the durability and integrity of the joined materials. Resistance welding is extensively employed in the automotive and construction industries due to its ability to deliver consistent and reliable welds on thin metals.
Similar to other welding methods, resistance spot welding has its limitations. It is most effective on thin metal sheets and may not be suitable for thicker materials. Additionally, the process requires access to both sides of the metal being welded, which can restrict its use in certain applications.
Resistance spot welding is a top choice for industries where speed, efficiency, and strength are critical despite these challenges. It is commonly used in automotive manufacturing and construction, where the ability to produce quick, strong welds on thin metal is essential.
View our Resistance Spot Welder
Stick Welding Machines
Stick welding, also known as Shielded Metal Arc Welding (SMAW), is widely used due to its simplicity and versatility. This process involves using a consumable electrode coated in flux. When an electric current passes through the electrode, it creates an arc between the electrode and the metal, melting both to form a weld. The flux coating on the electrode produces a gas that shields the weld from contaminants.
One of the main advantages of stick welding is its straightforward nature, making it accessible for beginners. The equipment required is relatively inexpensive compared to other welding methods, making it a cost-effective choice for many applications. Additionally, stick welding is highly versatile and can be used on a variety of metals, including steel, cast iron, and aluminum, making it suitable for a wide range of projects.
Stick welding does have some drawbacks. The process produces slag, a byproduct that must be chipped away after welding, adding an extra step. The skill level required to produce clean and aesthetically pleasing welds can be higher than other methods. The welds can also appear rough and require additional finishing.
For outdoor welding, heavy metal welding, and general repairs, stick welding is a reliable choice. Its ability to perform well in different conditions, including windy environments, makes it a favorite among many welders.
Flux-Cored Arc Welding Machines
Flux-Cored Arc Welding (FCAW) is a versatile and efficient welding method that uses a tubular wire filled with flux. This wire serves as both the electrode and the filler material. As the wire melts, the flux generates a gas that shields the weld from contamination. This process can be used with or without an external shielding gas, making it adaptable to different environments.
One of the significant advantages of FCAW is its effectiveness on dirty or rusty materials. The flux core helps clean the base metal, making it ideal for less-than-perfect surfaces. Additionally, the portability of FCAW equipment allows welders to work in various locations, including outdoors. Another benefit is the speed of the process, as it can produce high-quality welds quickly, which is essential in construction and heavy equipment repair.
FCAW does have some disadvantages. The process generates more smoke and fumes compared to other welding methods, which can be a health hazard if proper ventilation is not provided. The precision of the welds can also be less than methods like TIG welding, making it less suitable for projects requiring high accuracy. Additionally, the cost of the flux-cored wire is higher than solid wire, which can add to the overall expense.
FCAW is well-suited for construction, heavy equipment repair, and outdoor projects where speed, portability, and the ability to weld on dirty or rusty materials are crucial.
Plasma Arc Welding Machines
Plasma Arc Welding (PAW) is a high-precision welding method that uses a high-velocity jet of ionized gas, or plasma, to melt and join metals. The process is similar to TIG welding but with an added plasma arc, allowing for greater control and precision. This method is particularly useful for welding thin materials and producing high-quality welds.
The primary advantage of plasma welding is its precision. The focused plasma arc provides a high level of control, resulting in exceptionally clean and accurate welds. This makes it ideal for applications where high-quality welds are necessary, such as in the aerospace industry. PAW’s versatility allows it to be used on a variety of metals, including those that are difficult to weld with other methods, such as titanium and superalloys.
PAW is not without its challenges. The complexity of the equipment and the process requires a high level of skill and experience, making it less accessible for beginners. The cost of PAW machines and their maintenance can also be significant, which might be a consideration for some users. Additionally, the availability of PAW equipment can be limited compared to more common welding methods.
For high-precision projects, especially in industries like aerospace and for welding thin metal materials where the highest quality is essential, PAW remains a top choice.
How to Choose the Right Welding Machine
Selecting the right welding machine is crucial for ensuring the success and efficiency of your projects. With various options available, it’s important to consider several factors to make an informed decision that meets your specific needs.
Material Compatibility
The type of material you plan to weld significantly influences your choice of welding machine. Different machines are suited for different metals. For instance, MIG and TIG welders are excellent for welding aluminum and stainless steel, while stick welders are better suited for thicker materials like cast iron and steel. If your projects involve various metals, a versatile machine might be the best option.
Project Scale
For smaller, detailed work such as intricate automotive repairs or artistic metalwork, a TIG welder’s precision shines. Larger construction projects or heavy equipment repairs benefit from stick welders or flux-cored arc welders, which handle thicker materials and perform well outdoors.
Cost Considerations
Welding machines vary widely in cost. High-end models offer advanced features and greater durability but come with a higher price tag. Balance your budget with the quality and features you need. Investing in a more expensive, durable machine may be cost-effective in the long run for frequent use or professional projects.
Skill Level
Your experience and skill level play a significant role in choosing a welding machine. MIG welders are beginner-friendly, making them ideal for those learning the ropes. Assess your comfort and proficiency with different welding techniques to choose a machine that matches your capabilities.
Practical Steps
- Identify Your Needs: Define project types, considering the materials, size, and specific welding tasks required.
- Set a Budget: Determine your spending limit, factoring in the initial purchase price and ongoing costs.
- Evaluate Your Skill Level: Choose a machine that aligns with your proficiency level to ensure effective and safe use.
- Research Options: Investigate various types of welding machines, considering their advantages, drawbacks, and applications. Read reviews, and compare features.
- Consider Future Needs: Think about long-term goals. Will you expand your skills or take on diverse projects?
- Test and Compare: Whenever possible, try different machines to gauge operation and performance.
- Make Your Decision: Based on your research and testing, select the welding machine that best fits your needs, budget, and skill level.
By carefully considering these factors and following these steps, you can select the right welding machine to achieve high-quality results in your welding projects.
Conclusion
Choosing the right welding machine is essential for ensuring the success and efficiency of your projects. Remember, understanding the different types of welding machines—such as MIG, MAG, TIG, resistance spot welding, stick welding, flux-cored arc welding, and plasma arc welding, empowers you to make informed decisions tailored to your specific requirements.
Assessing factors like material type, project size, budget, and skill level is crucial when selecting the appropriate welding machine. Whether you’re a beginner or an experienced welder, there’s a machine that fits your requirements and enhances the quality of your work.
Explore the wide range of advanced welders offered by Car-O-Liner to find the perfect match for your welding needs. Visit our product pages to learn more about our innovative welding solutions and take the next step toward achieving precision and excellence in your welding projects.