Precision is essential in modern welding, particularly in automotive and industrial applications where quality and efficiency drive success. Pulse MIG welding delivers on both fronts, combining advanced control with reliable results by allowing for cleaner welds, minimized distortion, and improved precision when working with heat-sensitive materials.
This article outlines the fundamentals of pulse MIG welding, its applications, and how it benefits industries requiring precise and efficient performance. As a leader in collision repair and welding technology, Car-O-Liner leverages decades of expertise to support professionals with equipment designed for precision and reliability.
What is a Pulse MIG Welder?
By alternating between high and low current phases, a pulse MIG welding machine reduces spatter, distortion, and other defects that compromise weld quality. It offers a specialized solution for automotive and industrial applications, applying advanced waveform modulation to control heat input.
Unlike conventional MIG welding, which maintains steady parameters, pulse MIG welding strategically varies the current. This controlled spray-transfer approach directs molten droplets precisely, improving weld pool stability. The welder’s electronics ensure peak currents form droplets, while lower background currents sustain the arc, balancing penetration with minimized heat damage.
The result is a more refined process that’s especially valuable when working with delicate automotive panels, thin aluminum sheets, stainless steel components, or mild steel sections requiring uniformity. It addresses common issues like burn-through and structural weakening, enabling technicians to maintain appearance, integrity, and compliance with manufacturer specifications.
From collision repair shops that restore modern vehicle frames to industrial sectors demanding exceptional precision, pulse MIG technology elevates standards. Instead of spending hours correcting defects, professionals can produce welds that meet strict criteria from the start, streamlining production while ensuring components function safely in their intended environments.
Another advantage is adaptability. A pulse MIG welder can transition seamlessly across materials and thicknesses, making it an essential tool in versatile workshops. The refined arc control means less time adjusting parameters manually. Instead, synergic settings and intelligent feedback systems optimize the welding process, freeing operators to focus on craftsmanship.
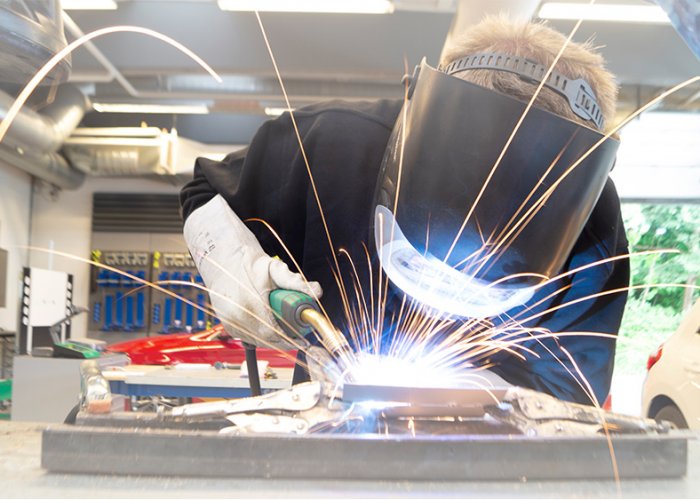
How Pulse MIG Welding Works
Pulsed welding relies on a carefully engineered electrical waveform. The welder creates a background current that maintains the arc between the wire and the workpiece. The unit then sends a higher current, or “pulse”, that makes contact with the metal droplet and propels it across the arc to the weld pool.
Spray pulse welding (also known as pulsed spray transfer) uses a much smaller gap between the background and peak currents than the large spikes seen in short circuit transfer. This smaller difference means that less energy is used, so less heat is generated during welding. As a result, this method is ideal for heat-sensitive materials such as aluminum and ultra-high strength steel (UHSS) and reduces the risk of warping thinner sheet metal. In addition, the alternating current pattern in this process produces a uniform transfer of droplets, ensuring a consistent weld zone.
The welder’s digital interface manages the pulses, allowing the unit to control the size of the droplets, the frequency, and the amount of filler material being applied, which also affects the amount of heat. By entering a few criteria such as workpiece thickness and wire type, the machine optimizes the parameters to achieve the desired results.
Such automated intelligence lowers the barrier to entry. While there’s still a learning curve, operators no longer spend hours experimenting. The machine’s internal database of preset programs ensures consistent results. Welding mild steel or sensitive alloys like aluminum and stainless steel becomes a straightforward process guided by data-driven optimization.
Compared to TIG welding, pulse MIG offers higher deposition rates and faster travel speeds. TIG relies on a manually fed tungsten electrode and requires significant skill to achieve clean results on thin materials. Pulse MIG, on the other hand, integrates advanced controls to deliver precision without sacrificing productivity.
Distinguishing it further from stick welding or conventional MIG methods, pulse MIG optimizes arc stability and reduces fume generation. By refining the droplet transfer, it minimizes erratic spatter and inconsistent penetration. This allows for better weld quality right out of the torch, cutting down on extensive post-weld finishing tasks.
Pros and Cons of Pulse MIG Welding
Pros of Pulse MIG Welding
The first advantage is improved weld quality. Controlled droplet of MIG welding transfer leads to deeper, more uniform penetration without oversaturating the weld pool with heat. This reduces the likelihood of porosity, inclusions, and cracking, resulting in durable joints that maintain their integrity under stress and over extended service life.
Pulse MIG welders can deposit more material per unit time than many alternative processes, improving welding speed. Faster travel speeds let technicians handle larger volumes or more complex assemblies efficiently, transforming what might have been a time-consuming operation into a streamlined task.
By carefully managing heat input, pulse MIG welding keeps thin metals from warping or buckling which is essential when working with delicate aluminum automotive panels or stainless steel assemblies that demand precise geometries. Reduced rework saves time, materials, and operating costs.
Pulse MIG equipment often includes synergic control features that simplify parameter selection. Operators can input basic information like base metal type and wire diameter and the welder automatically sets voltage, wire speed, and pulse frequency.
Beyond automotive work, the same advantages translate well into industrial fabrication, aerospace assemblies, and marine applications. In fact, any environment that values minimal finishing, tight tolerances, and robust joint properties benefits from the pulse MIG welding.
Cons of Pulse MIG Welding
Despite its benefits, pulse MIG welding also presents certain limitations that must be considered. Advanced electronics, waveform controls, and synergic programming often translate into a steeper price tag. Smaller workshops or those with limited budgets might hesitate before investing in technology that requires both capital and training commitments.
Another challenge is the learning curve because mastering the nuances takes time. Although synergic controls simplify many aspects, operators must understand how changing pulse frequency or current affects the weld. Without proper instruction, technicians might struggle to fully leverage the equipment’s capabilities, slowing the transition to optimized production.
The availability of machine-specific consumables or spare parts can also be a concern. High-end welders with proprietary features may limit flexibility if sourcing components proves difficult. Ensuring supplier support and robust service networks is advisable before committing to a specific pulse MIG welding system.
8 Reasons to Use a Pulse MIG/MAG Welder in Your Workshop
1. Reduced Heat Input and Minimal Distortion
One of the biggest advantages of pulse welding is its ability to control heat input. Unlike traditional welding methods, pulse welding operates by alternating between a high and low current, preventing excessive heat buildup. This results in less distortion and warping, making it an excellent choice for welding thin materials, aluminum and stainless steel.
2. Improved Weld Penetration and Strength
Pulse welding allows for deeper weld penetration without overheating the metal. The controlled bursts of high current create strong, durable welds while maintaining the integrity of the material. This makes it ideal for applications that require structural strength, which is required inside the collision repair industry.
3. Reduced Spatter and Cleaner Welds
Spatter is a common issue in conventional welding, requiring additional cleaning and post-weld finishing. Pulse welding minimizes spatter formation, leading to smoother, cleaner welds with little to no need for rework. This enhances efficiency and productivity, reducing labor time and costs associated with cleaning and finishing processes.
4. Better Control Over Difficult Metals
Certain metals, like aluminum and stainless steel, can be challenging to weld due to their thermal conductivity and oxidation properties. Pulse welding provides precise arc control, ensuring consistent, high-quality welds with minimal defects such as porosity or cracking. This makes it a preferred choice for industries where material integrity is critical.
5. Ideal for All Skill Levels
Because of its automated heat regulation, clean welds, and reduced defects, even less-experienced welders can achieve high-quality results with minimal effort. Advanced welders also benefit from its precision for critical applications.
6. Energy Efficiency and Cost Savings
Pulse welding is designed to optimize energy consumption, as it only uses high current when necessary. This controlled energy usage reduces power costs and minimizes material waste, making it an eco-friendly and cost-effective solution. In large-scale manufacturing, these savings can be significant, improving overall operational efficiency.
7. Enhanced Aesthetic Finish
For applications where appearance matters, such as automotive body panels, decorative metalwork, pulse welding provides superior aesthetics. The reduced spatter and controlled weld pool result in smooth, visually appealing welds that require minimal finishing.
8. Versatility Across Different Materials and Thicknesses
Pulse welding is highly adaptable, making it suitable for a wide range of materials and thicknesses. Whether working with thin aluminum sheets or thick structural steel, the controlled heat input ensures precise and high-quality welds. This versatility makes pulse welding a valuable tool across various industries.
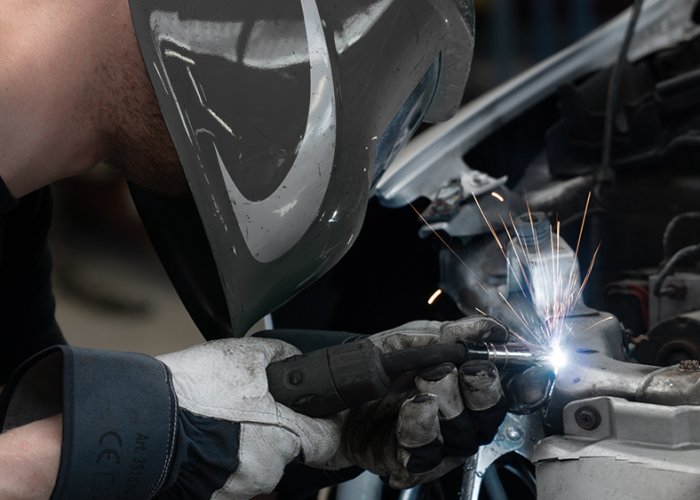
Key Considerations When Choosing a Pulse MIG Welder
Evaluating pulse modes is crucial. Single-pulse welding alternates currents, providing stable droplet transfer for standard applications. Double-pulse MIG adds a secondary modulation of the wire feed speed, improving bead aesthetics with a TIG-like appearance. The double pulse also acts as a thermal pause further helping to control heat affect.. Shops focusing on cosmetic welds or high-end work often prioritize models offering versatile pulse modes.
Power requirements should align with project scope. Single-phase machines may suffice for smaller shops and thinner materials, while three-phase units deliver the power needed for thicker sections. Welders that are capable of running on either single or three phase provide versatility, especially when dealing with a shop’s existing electrical facilities. Matching the machine’s output capacity with production demands ensures reliability, prevents overload, and keeps operating costs manageable.
Material compatibility is non-negotiable. Automotive repairs often involve a range of metals, including high-strength steels and aluminum alloys. A pulse MIG welder designed to handle multiple wire types, diameters, and shielding gases provides the flexibility to tackle diverse tasks, accommodating evolving industry standards and customer requests.
Advanced synergic features streamline workflow. By selecting a preset program, operators ensure that voltage, wire speed, and pulse frequency are automatically adjusted. This not only saves time but also reduces the likelihood of errors. Shops handling large volumes appreciate the consistency and repeatability these automated programs provide.
Consider availability of training, technical support, and documentation. Even the most intuitive machines benefit from guidance. Well-structured training modules, online tutorials, and responsive customer service help operators understand nuanced settings like pulse frequency adjustments or double-pulse modes, ensuring they can harness the full potential of their equipment. Durability and serviceability also matter. Investing in a reputable brand like Car-O-Liner ensures access to parts, upgrades, and service technicians.
Before finalizing a purchase, evaluate real-world performance by consulting peers, reading case studies, and possibly arranging demonstrations. Understanding how a specific welder handles typical projects like repairing aluminum frames or welding mild steel panels helps confirm that it meets quality, speed, and flexibility targets set by your operation.
Ultimately, the choice boils down to balancing cost, complexity, and the range of capabilities required. A carefully selected pulse MIG welder can yield substantial returns, enabling shops to expand their service offerings, improve quality, and deliver results that resonate with manufacturers, insurers, and end-customers alike.
Comparing Pulse MIG to Conventional Methods
Conventional MIG welding suits many tasks but struggles with thin or heat-sensitive materials. Pulse MIG improves droplet transfer and stability, resulting in less finishing work. Reducing defects at the source means fewer hours spent correcting issues, which translates into consistent quality and lower long-term operational expenses.
Stick welding has historically been reliable for fieldwork but falls short in environments demanding polished aesthetics and lightweight joints. Pulse MIG offers more refined control, producing visually appealing welds with less spatter. This difference elevates the final product’s look while maintaining mechanical integrity and strength.
Short circuit metal transfer welding techniques remain prevalent, but pulse MIG’s dynamic current modulation surpasses these static methods. The ability to customize pulse frequency and waveform shape delivers refined outcomes on complex materials. While short circuit transfer remains useful in certain niches, pulse MIG’s versatility is increasingly attractive to modern operations.
Conclusion
Pulse MIG welding represents a significant advancement in joining technology. By leveraging waveform modulation, synergic controls, and adjustable pulse frequencies, it solves long standing challenges like distortion and poor weld quality. Ideal for automotive collision repair and beyond, it empowers technicians to produce stronger, cleaner, and more efficient welds.
As materials evolve and industries embrace lighter alloys, pulse MIG remains a crucial enabler. With fewer post-weld refinishing steps, lower defect rates, and faster throughput, shops gain a competitive edge. A well chosen pulse MIG welder secures the adaptability needed to address tomorrow’s fabrication and repair demands.
Car-O-Liner’s CMI 300 Pulse exemplifies this technology’s potential. Designed with professionals in mind, this system combines intuitive interfaces and double-pulse options. Investing in such equipment ensures that shops meet evolving standards, achieve remarkable quality, and confidently tackle the most challenging welding tasks.